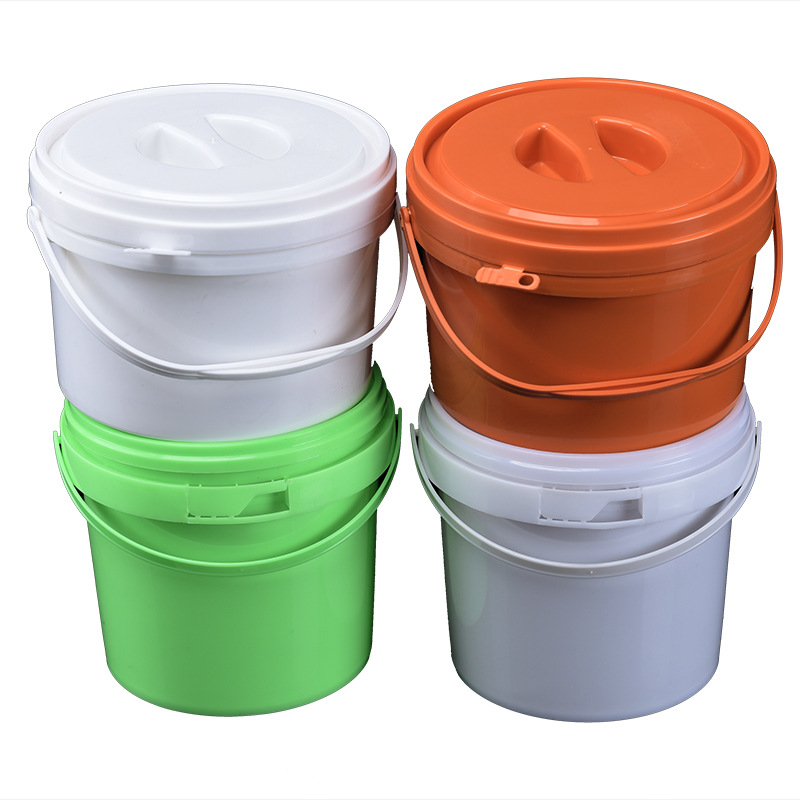
このページの内容は予告なく変更することがあります。
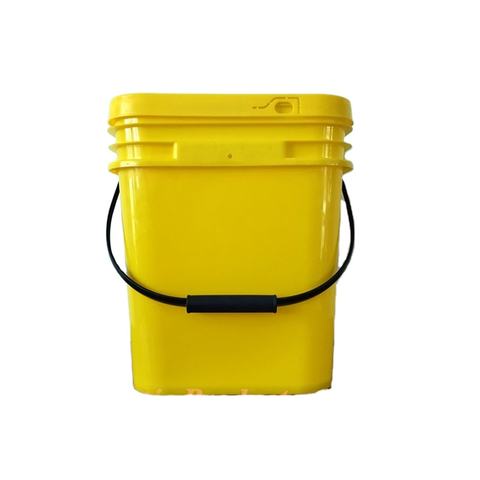
プレミアム工業用ペイントバケツ:プロ級PP/HDPEプラスチック容器
1Lから25Lまでカスタマイズ可能な工業用プラスチックペイントバケツのトップメーカー。漏れ防止シール、耐久性のあるハンドル、耐薬品性材料などの特徴があります。塗料、化学薬品、食品、工業用途に最適です。カスタムブランドによる大量卸売も可能。
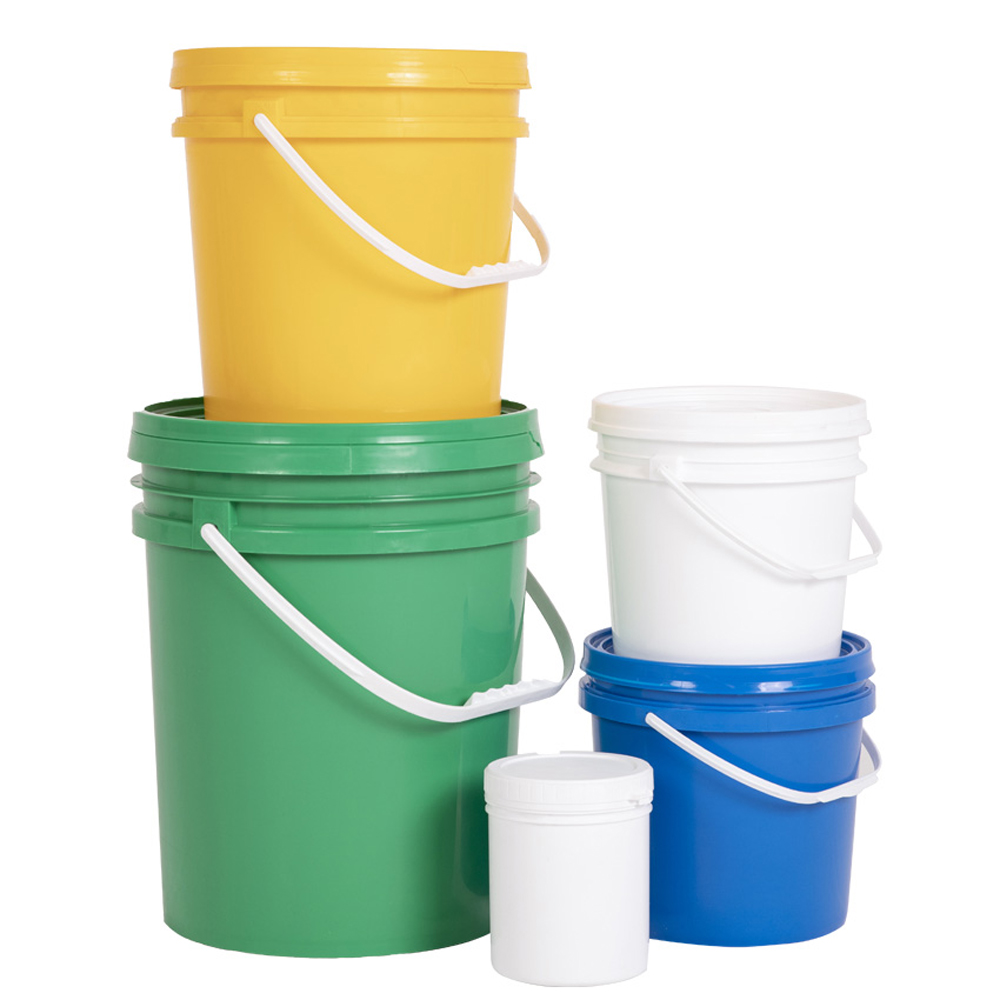

食品の長期保存に最適なPackagingBucketは?
2024年における鳥の種バケツ生産の包括的分析。材料、製造工程、安全基準、持続可能性の実践を網羅。業界の専門家やメーカーにとって不可欠なガイドブック。