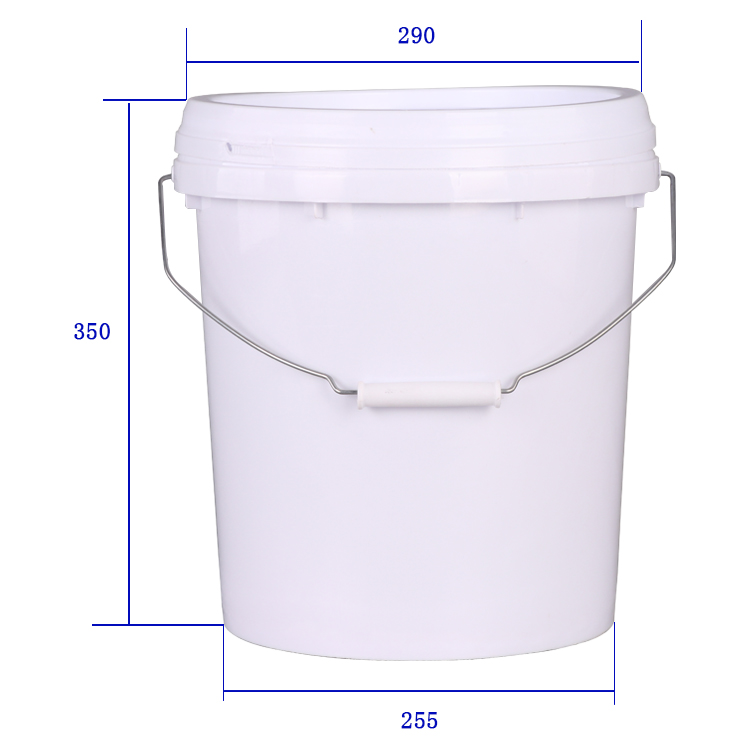
로렘 입섬 돌로르 시트 아멧, 컨설턴트 아디피싱 엘리트, 세드 도 이우스모드 로렘 입섬 돌로르 시트 아멧 컨설턴트 아디피싱 엘리트, 세드 도 이우스모드 로렘 입섬
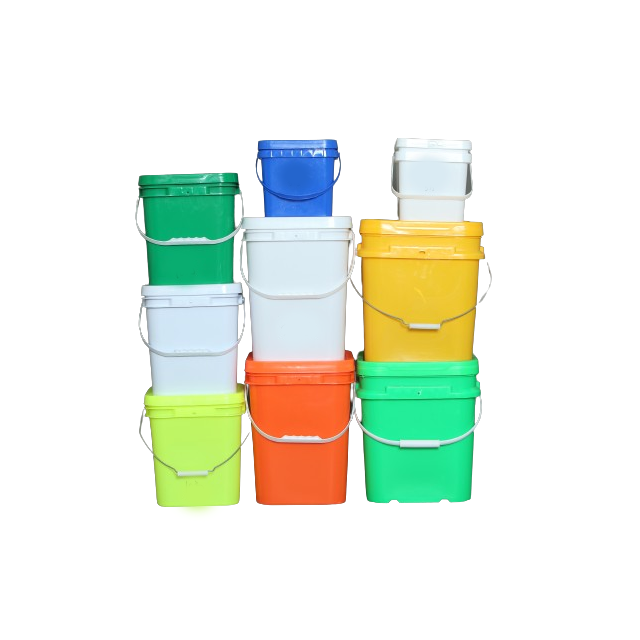
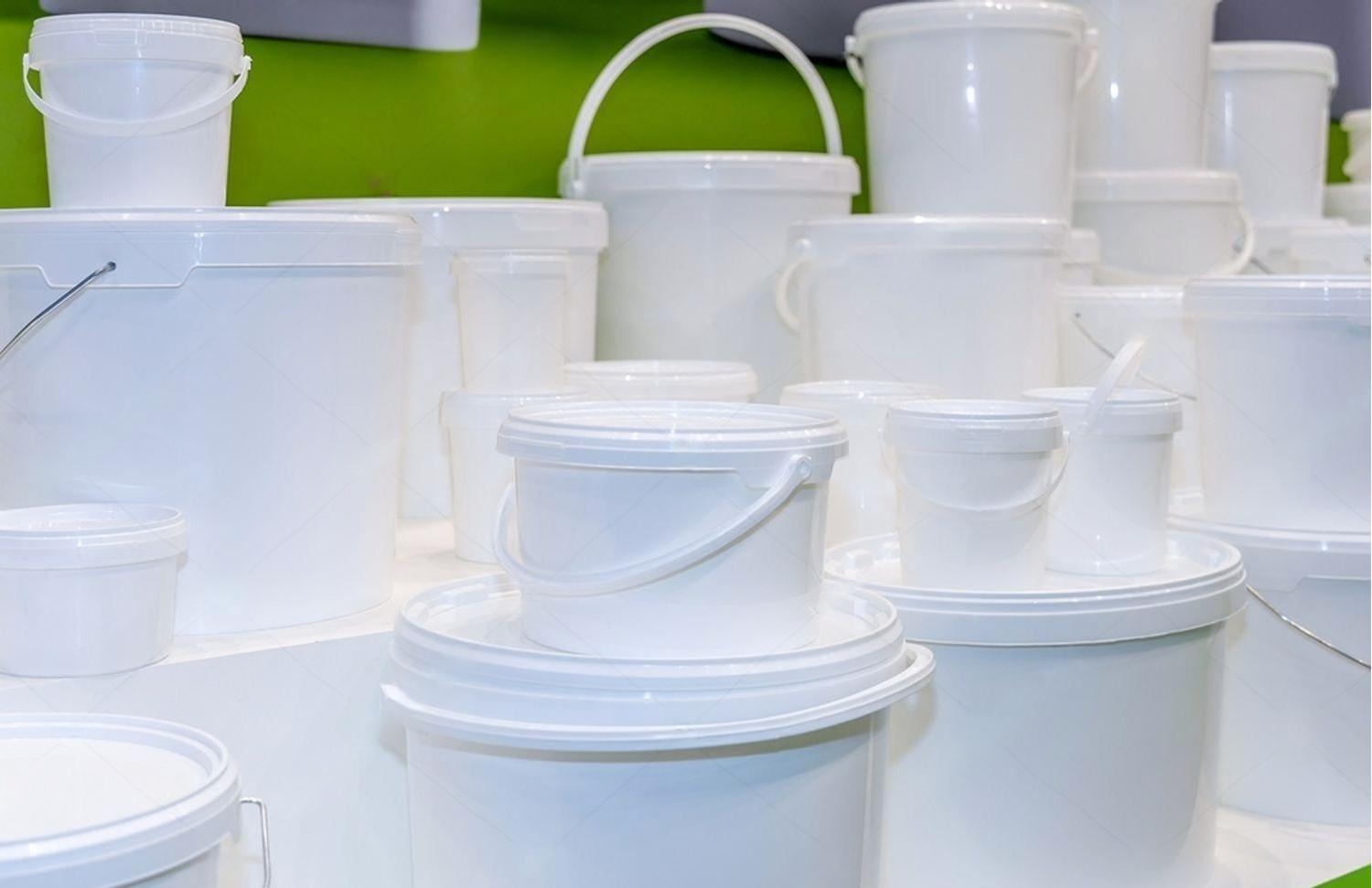
500ML Round Plastic Buckets: Compact Solutions for Big Impact
재료, 제조 공정, 안전 표준 및 지속 가능성 관행을 포함한 2024년 조류 종자 통 생산에 대한 종합적인 분석입니다. 업계 전문가와 제조업체를 위한 필수 가이드입니다.
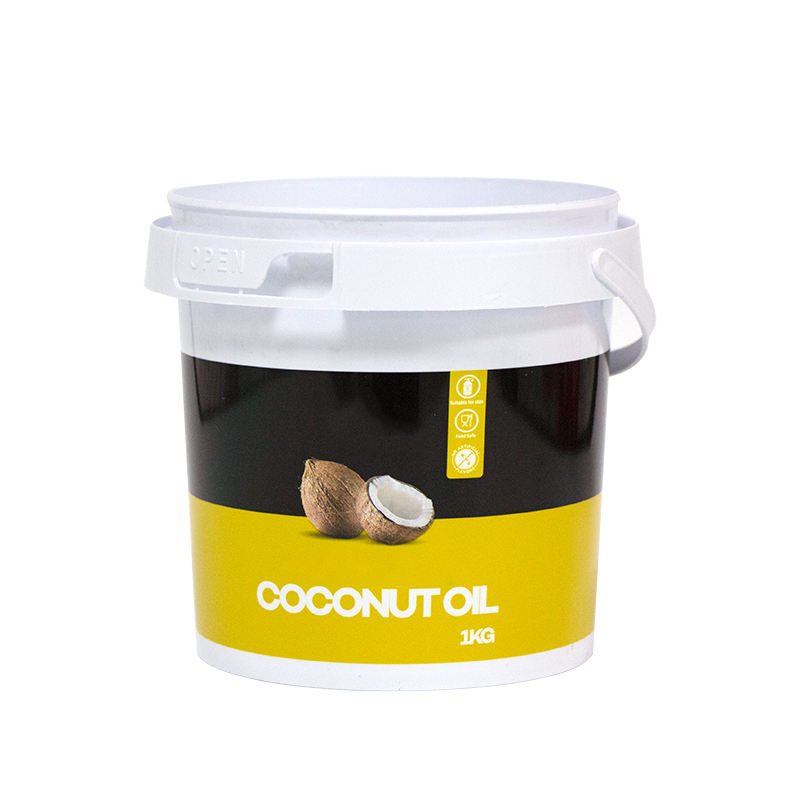
상업용 아이스크림 제조업체에 적합한 맞춤형 크기 (150ml-5L)의 도매 PP 플라스틱 버킷
식품에 안전한 PP 소재, 맞춤형 크기, IML 장식 옵션, 대량 도매 가격으로 제공되는 전문가용 아이스크림 포장 솔루션을 확인해 보세요. 뛰어난 보존성을 갖춘 믿을 수 있고 비용 효율적인 용기 솔루션을 찾는 아이스크림 제조업체, 유통업체 및 식품 서비스 기업에 적합합니다.