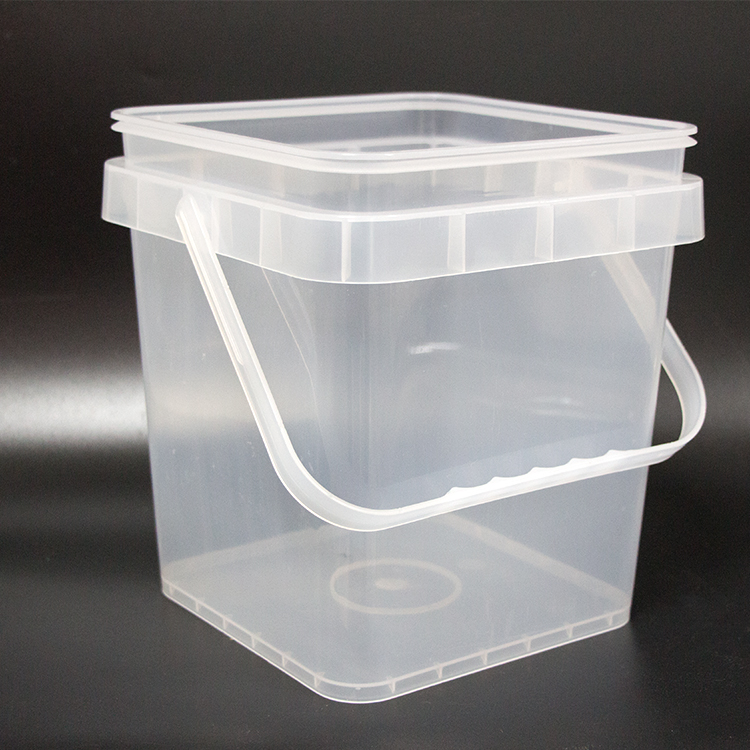
Lorem ipsum dolor sit amet consectetur adipiscing elit, sed do eiusmod Lorem ipsum dolor sit amet consectetur adipiscing elit, sed do eiusmod lorem ipsum
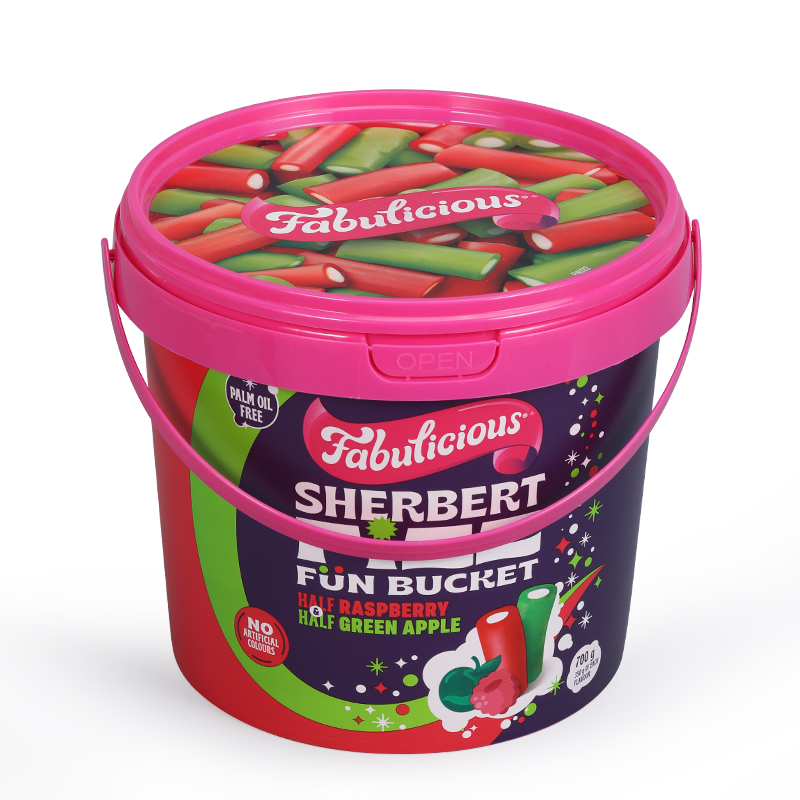
Fabricación ROI: Análisis de la cartera de tamaños de cubo redondo
Análisis exhaustivo de la producción de cubos de alpiste en 2024, que abarca materiales, procesos de fabricación, normas de seguridad y prácticas de sostenibilidad. Guía esencial para profesionales del sector y fabricantes.
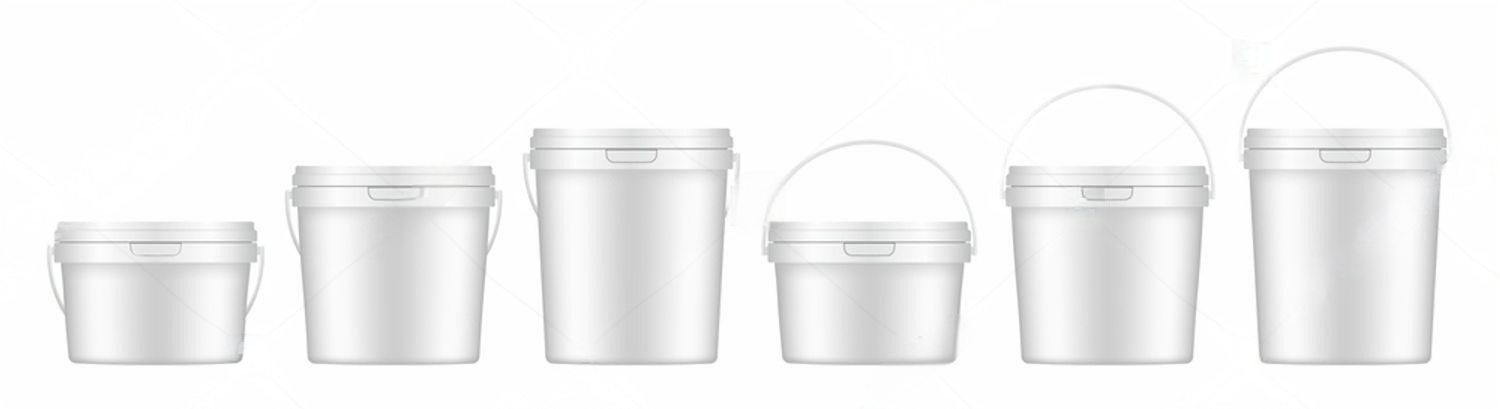
La importancia del control de calidad en la fabricación de cubos de envasado
Análisis exhaustivo de la producción de cubos de alpiste en 2024, que abarca materiales, procesos de fabricación, normas de seguridad y prácticas de sostenibilidad. Guía esencial para profesionales del sector y fabricantes.
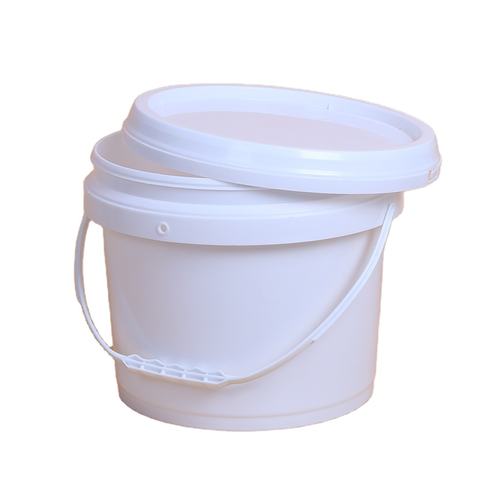
Producción de envases para encurtidos: Soluciones de fabricación
Análisis exhaustivo de la producción de cubos de alpiste en 2024, que abarca materiales, procesos de fabricación, normas de seguridad y prácticas de sostenibilidad. Guía esencial para profesionales del sector y fabricantes.