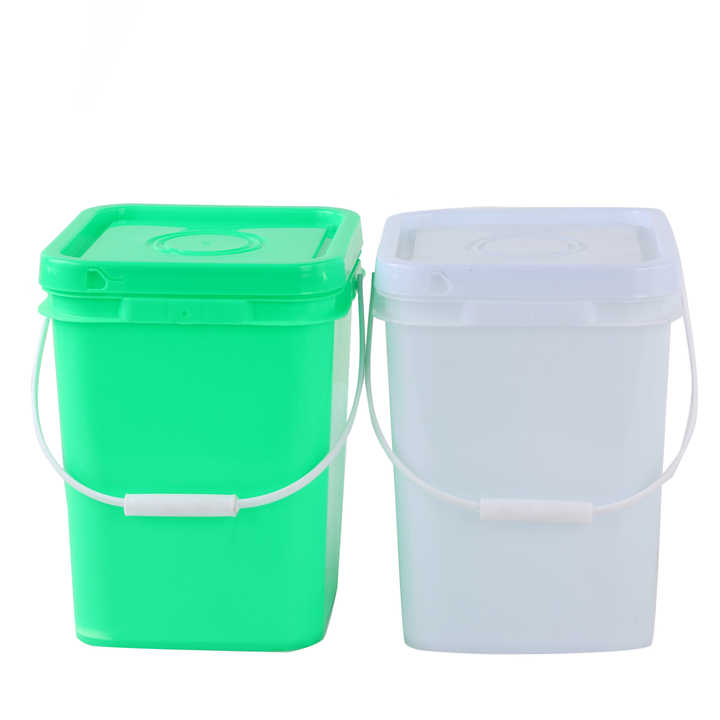
Lorem ipsum dolor sit amet consectetur adipiscing elit, sed do eiusmod Lorem ipsum dolor sit amet consectetur adipiscing elit, sed do eiusmod lorem ipsum
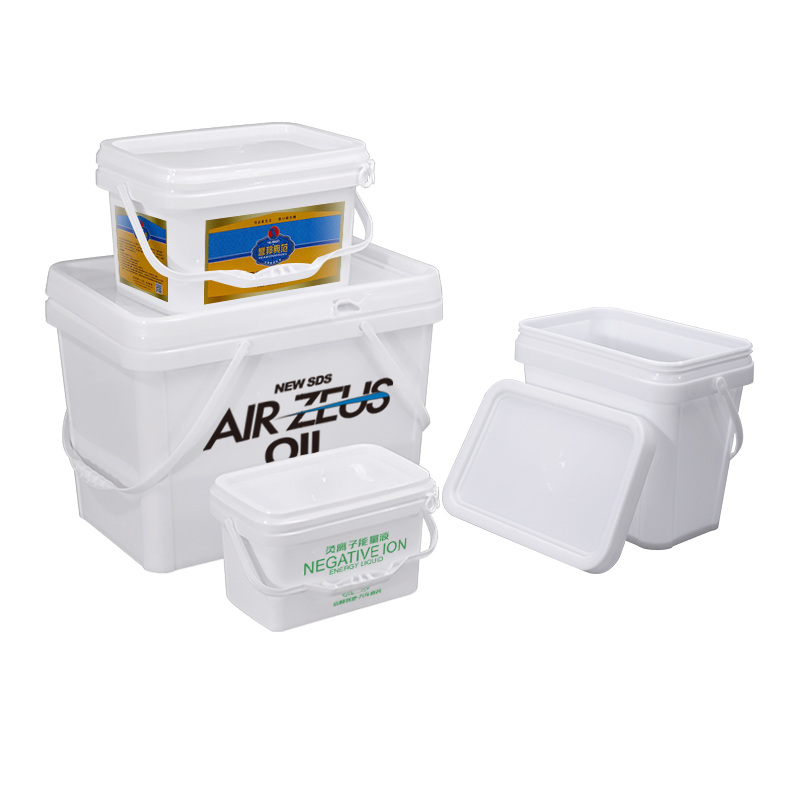
Fabricación de cubos cuadrados de alto rendimiento: La innovación se une a la excelencia industrial
Descubra los cubos cuadrados de plástico de primera calidad fabricados con la tecnología más avanzada de diseño de moldes. Nuestras soluciones de envasado alimentario ofrecen una durabilidad superior, tamaños personalizables de 2L-25L y cumplen las normas de seguridad internacionales. Perfectos para necesidades de envasado industrial, alimentario y químico.
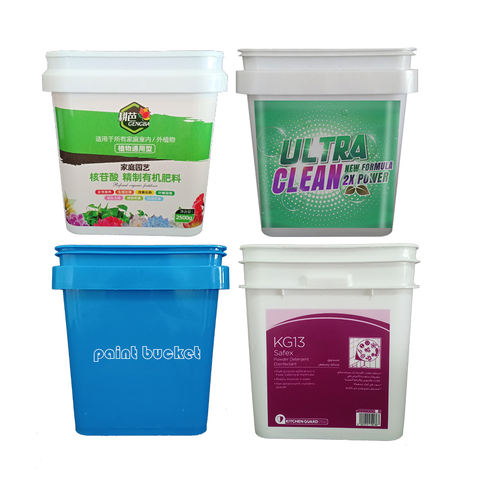
Guía completa para elegir el cubo de plástico ideal para sus necesidades
Inicio Índice Introducción Seleccionar el cubo de plástico adecuado es una decisión crítica que va más allá de una simple compra.
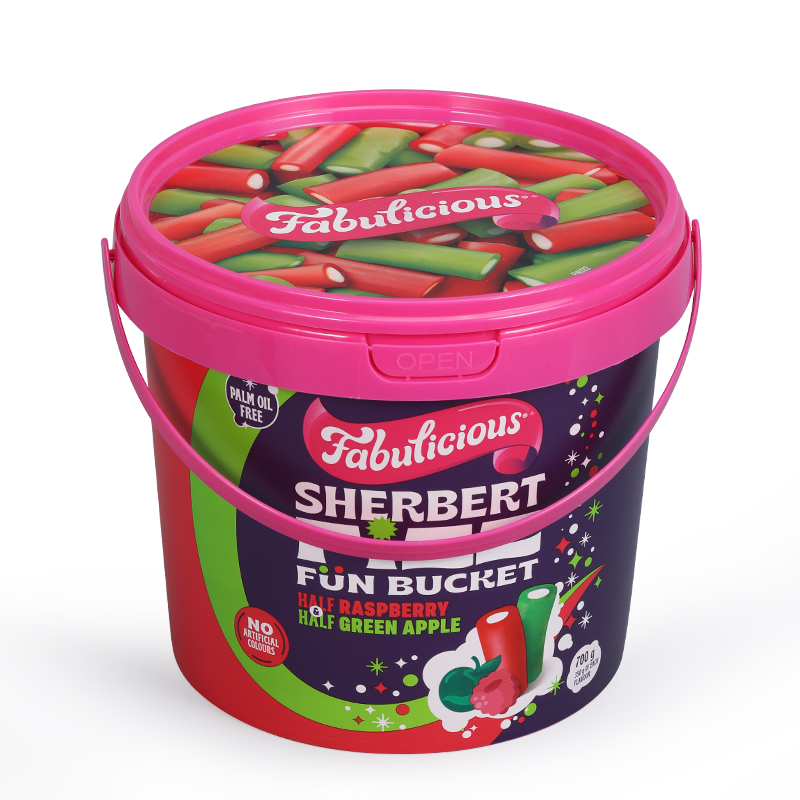
Fabricación ROI: Análisis de la cartera de tamaños de cubo redondo
Análisis exhaustivo de la producción de cubos de alpiste en 2024, que abarca materiales, procesos de fabricación, normas de seguridad y prácticas de sostenibilidad. Guía esencial para profesionales del sector y fabricantes.